
Home » Case-Study
Expert CNC Machining & Complete Fabrication Solutions
Specialize in fabrication processes tailored to OEM parts and assembly
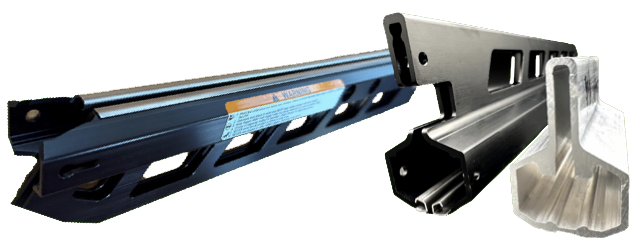
Step 1: Aluminum Extrusion
Aluminum extrusion is a versatile and cost-effective process that can be used to create a wide range of products. Our expert has years of experience in the field and can provide valuable insights into the process. They can also offer guidance on design and help ensure a successful outcome for your project.
Step 2: Control Extrusion Profile Dimension
Ensuring the quality of products is of utmost importance to meet the strict industry standards. For this, we rely on Coordinate Measuring Machine (CMM) dimensioning, which is a trusted and reliable approach. This method eliminates human errors and consistently produces superior quality products.
Step 3: CNC Machining Profile to Magazine
The use of CNC machining enables manufacturers to ensure that every cut and hole is made to exact specifications, thereby producing high-quality products with perfect consistency. Additionally, the process is fast and cost-effective, leading to larger production runs and faster turnaround times. With CNC machining, manufacturers can produce magazines with precise tolerances, ensuring that they fit snugly and function smoothly.
Step 4: Control Machining Dimension
The precise control of machining dimensions is of utmost importance in our manufacturing process. To ensure that the parts meet the required specifications and progress to the subsequent manufacturing stages, we employ advanced technical inspection machines. These machines are capable of accurately verifying the dimensions of the parts, thereby ensuring that they meet the required tolerances. This step is critical in maintaining the quality of our products and ensuring that they meet the highest standards of precision and accuracy.
Step 5: Polish surface flaws
Polishing surface flaws removes imperfections to achieve a smooth and lustrous finish. It's used in manufacturing and construction to enhance appearance and functionality. Various techniques and materials can be used depending on the surface and desired outcome.
Step 6: Anodizing Machined profile
Anodizing is an electrochemical process that creates a protective oxide layer on metal surfaces. It enhances corrosion resistance, durability, and aesthetics of machined profiles. It can be performed on various metals, and involves immersing the metal in an electrolytic solution and applying an electric current. Overall, anodizing is a versatile and effective method for improving the performance and appearance of machined profiles.
Step 7: Cosmetic Inspection
The cosmetic inspection process holds significant importance in our manufacturing operations, particularly for parts intended for end-users. This critical step ensures that the final product meets the desired aesthetic standards and is free from any defects or imperfections. As such, we prioritize this step in our production process to guarantee that our customers receive high-quality products that meet their expectations.
Step 8: Sheet Metal Forming Wear Channel
Sheet metal forming involves shaping and bending metal sheets into various forms and sizes. The wear channel is a crucial component that guides and supports the metal sheet during the forming process. It is made from durable materials such as steel or aluminum and is designed to withstand high pressures and stresses.
Step 9: Control Wear Channel dimensioning
We take great pride in our quality control measures, which are designed to identify and address any potential issues before they can impact the final product. Our dedication to quality is a testament to our unwavering commitment to customer satisfaction and our ongoing pursuit of excellence in all aspects of our business.
Step 10: Assemble the Wear Channel and labeling magazine
Our services extend beyond manufacturing to include assembly for our customers. We guarantee that all mating parts function without any defects. Our commitment to quality ensures that our customers receive a reliable and functional product.
What customer can get from our integration Fabrication?
Flexibility and Adaptability
With customizable features and automation, it streamlines operations and enhances performance for any sized business.
Enhanced Communication
We keep our customers informed from design to production, building trust and leading to repeat business.
Reduced Lead Time
With our expertise and technology, we deliver quality products quickly. Partnering with us means faster turnaround, reduced inventory costs, and greater supply chain flexibility.
Consistent Quality
We have a strict quality control system, top-of-the-line equipment, and skilled professionals, all working together to deliver products that meet or exceed your expectations.
Cost Saving
Our fabrication services save you money with efficient production, reduced labor costs, high-tech equipment, minimal waste, and great value.
Single Point of Accountability
From design to installation and maintenance, our team handles everything in-house, saving customers time and hassle while ensuring consistent quality.
All parts displayed on this website are intended solely to demonstrate our manufacturing capabilities and are not available for sale. no proprietary information or intellectual property of our customers is disclosed.