Case Studies
Home » Case Study 1
Mastering Complexity with Our CNC Machining Expertise:
4-Axis CNC Simultaneous Machining with Fully Engraved Parts
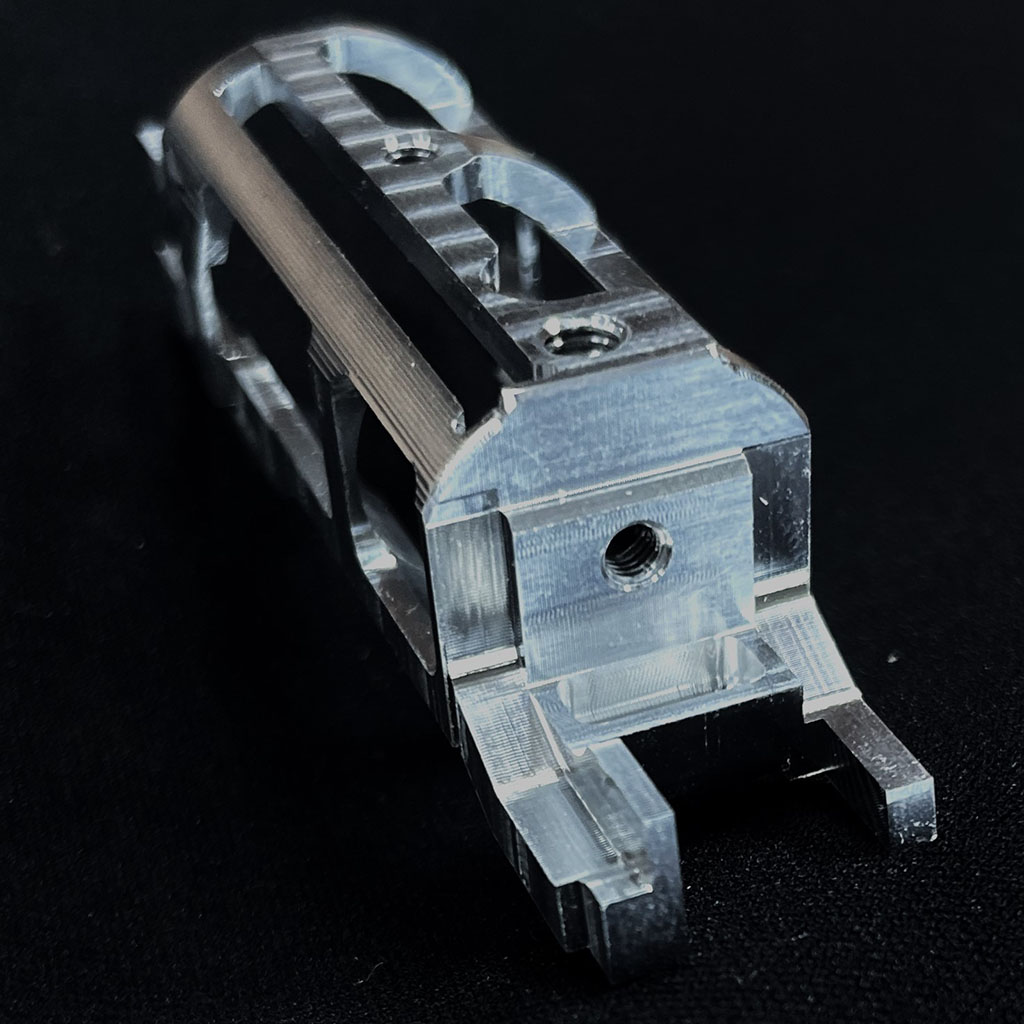
Workpiece Alignment vs. Fixture & Machine Coordinates
To ensure repeatability and consistency, the play between the workpiece and the fixture must be prevented. The fit between the fixture and the workpiece is precisely controlled within a tolerance of 0.01mm.

Strict dimension tolerance
.X +/-.3
.XX +/-.15
.XXX +/-.05
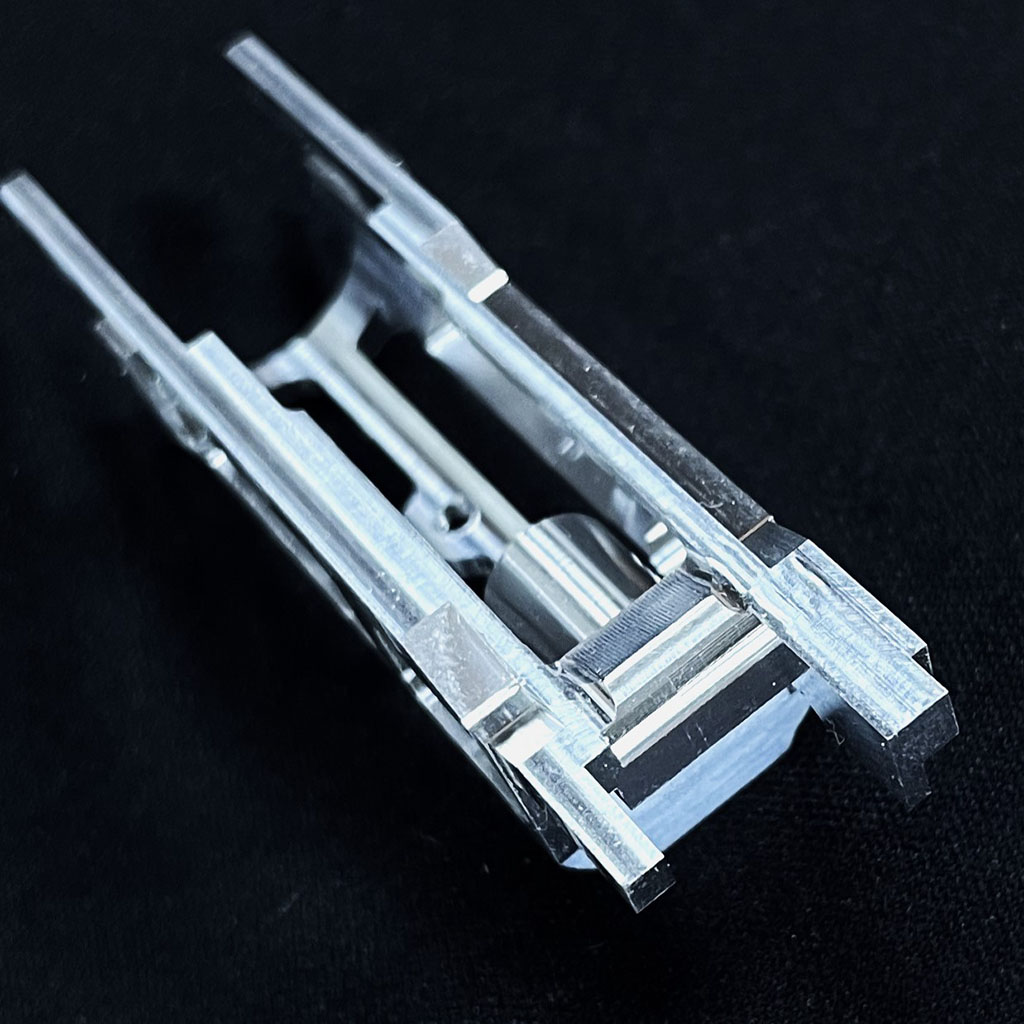
Deep Slot Machining
Machining a deep slot within the workpiece is highly challenging due to tool access limitations and the rigidity required of the cutting tool.
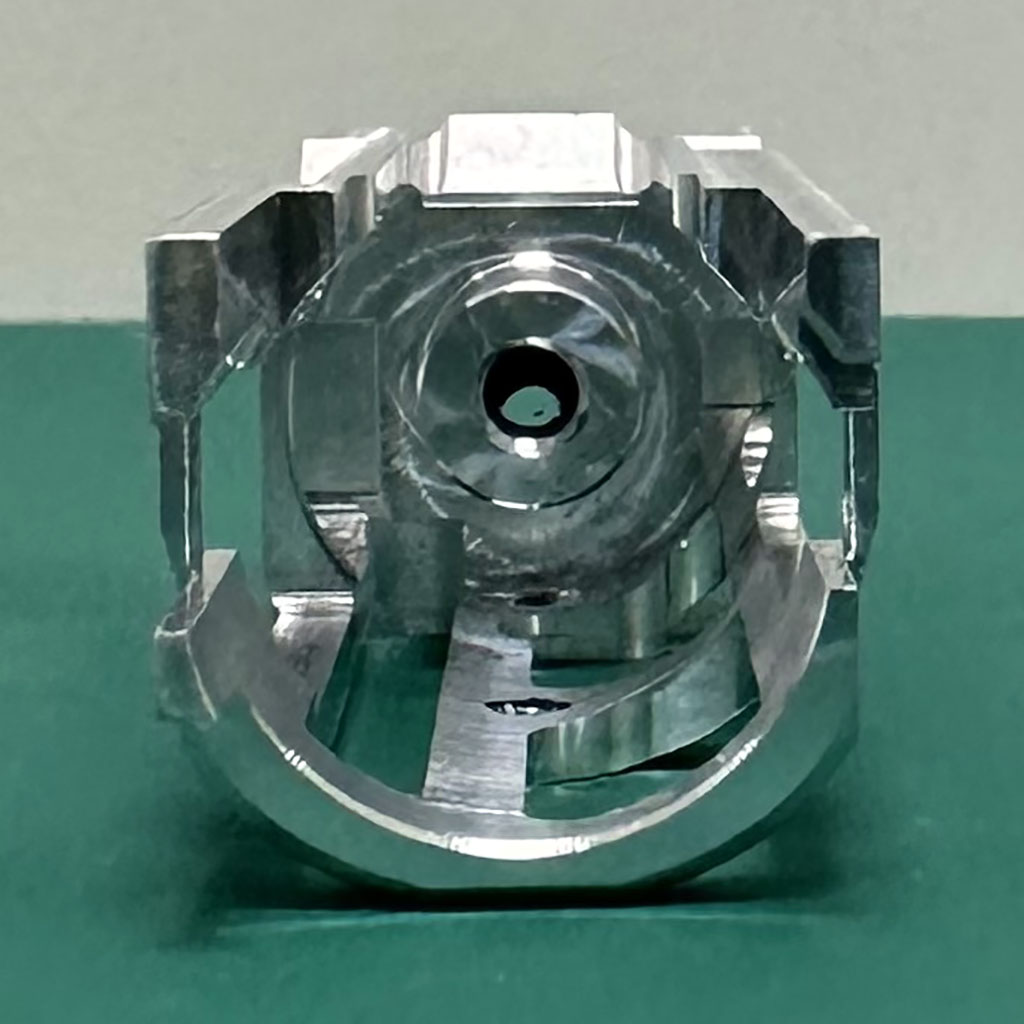
360-Degree
Machining Fixture
We created a specialized fixture that allows for comprehensive 360-degree CNC machining. This fixture enables access to all angles, ensuring uniformity and precision.

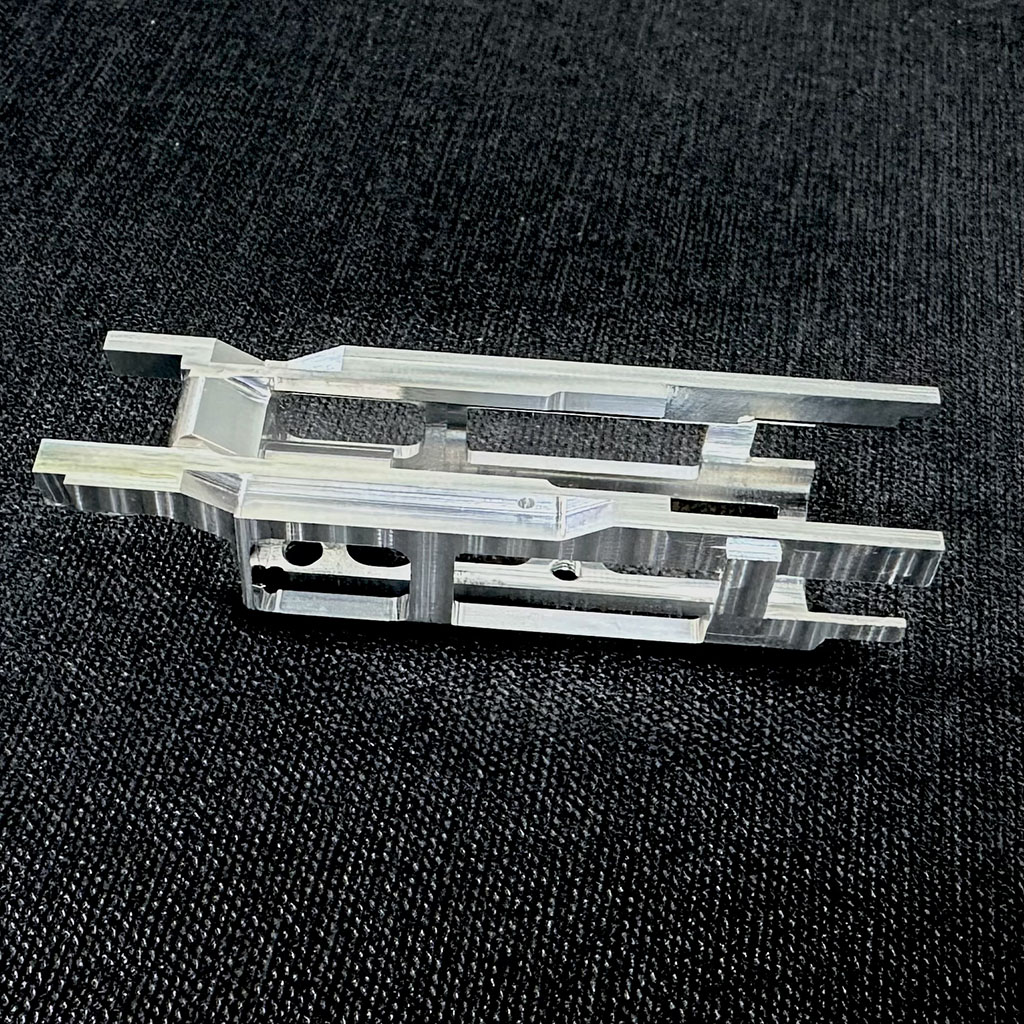
Advanced CNC Software
We invested in high-tech software capable of adapting to 5-axis CNC machining, enhancing our ability to handle intricate and precise machining tasks with greater efficiency and accuracy.
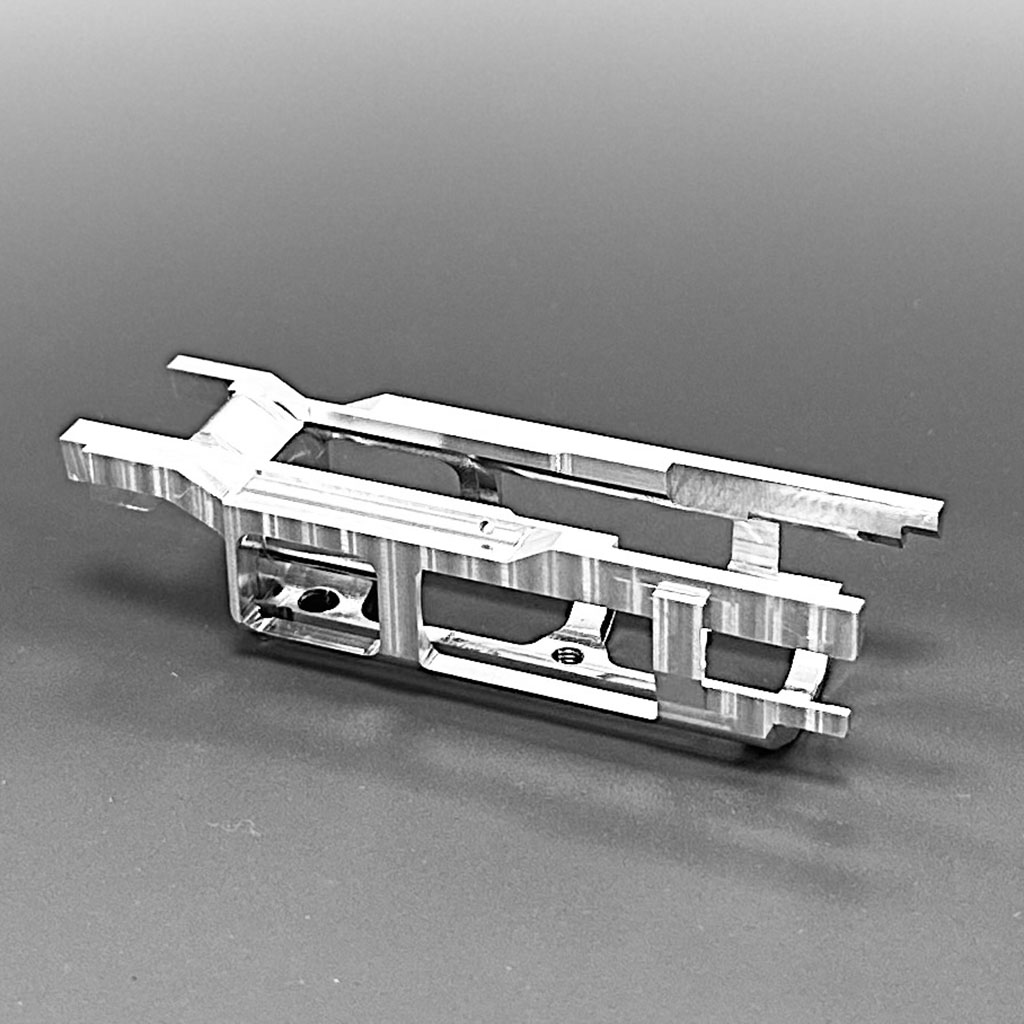
7075 Aluminum Machining
Machining 7075 aluminum alloy presents significant challenges due to its high internal stress, making it prone to warping and deformation.
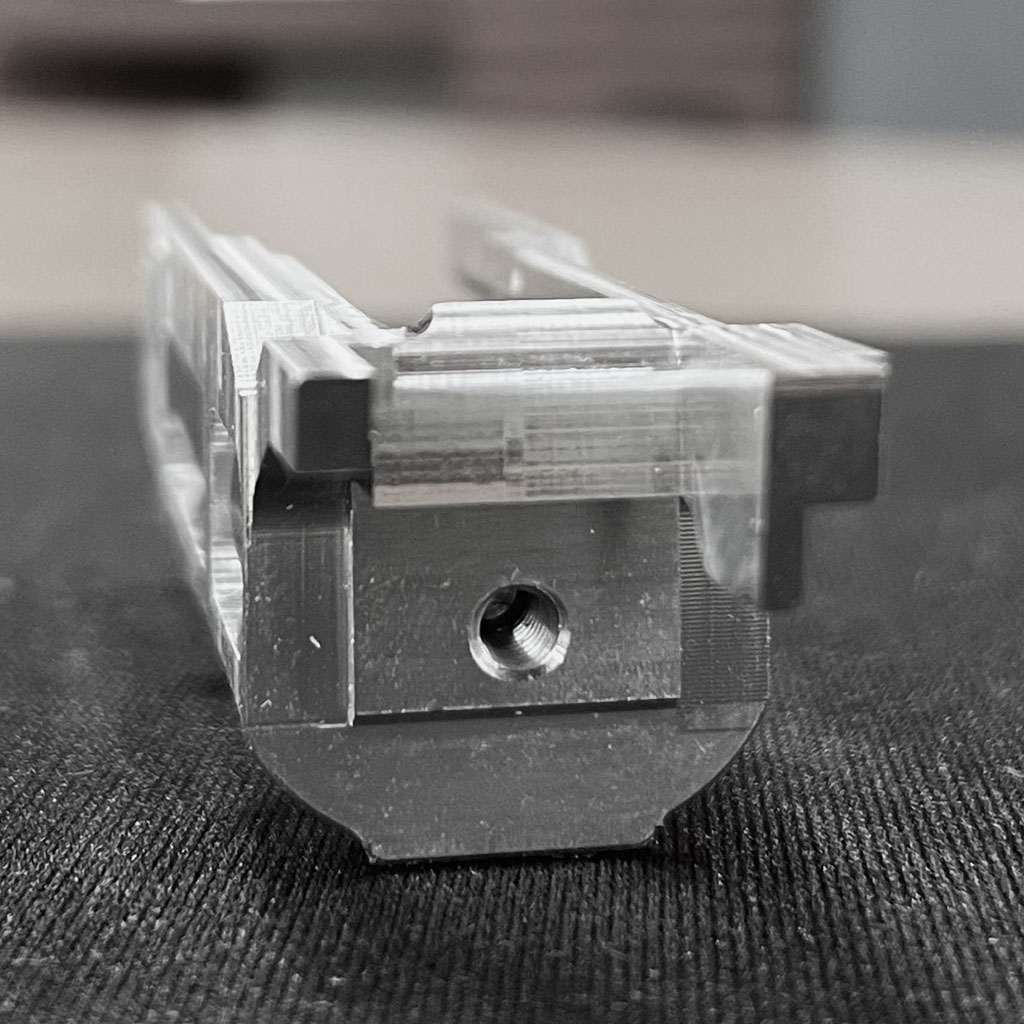
Precision Cutting Tool
We utilized a specialized cutting tool with dimensions of 4mm x 55mm for hole drilling, ensuring precise cuts and maintaining the material's integrity.
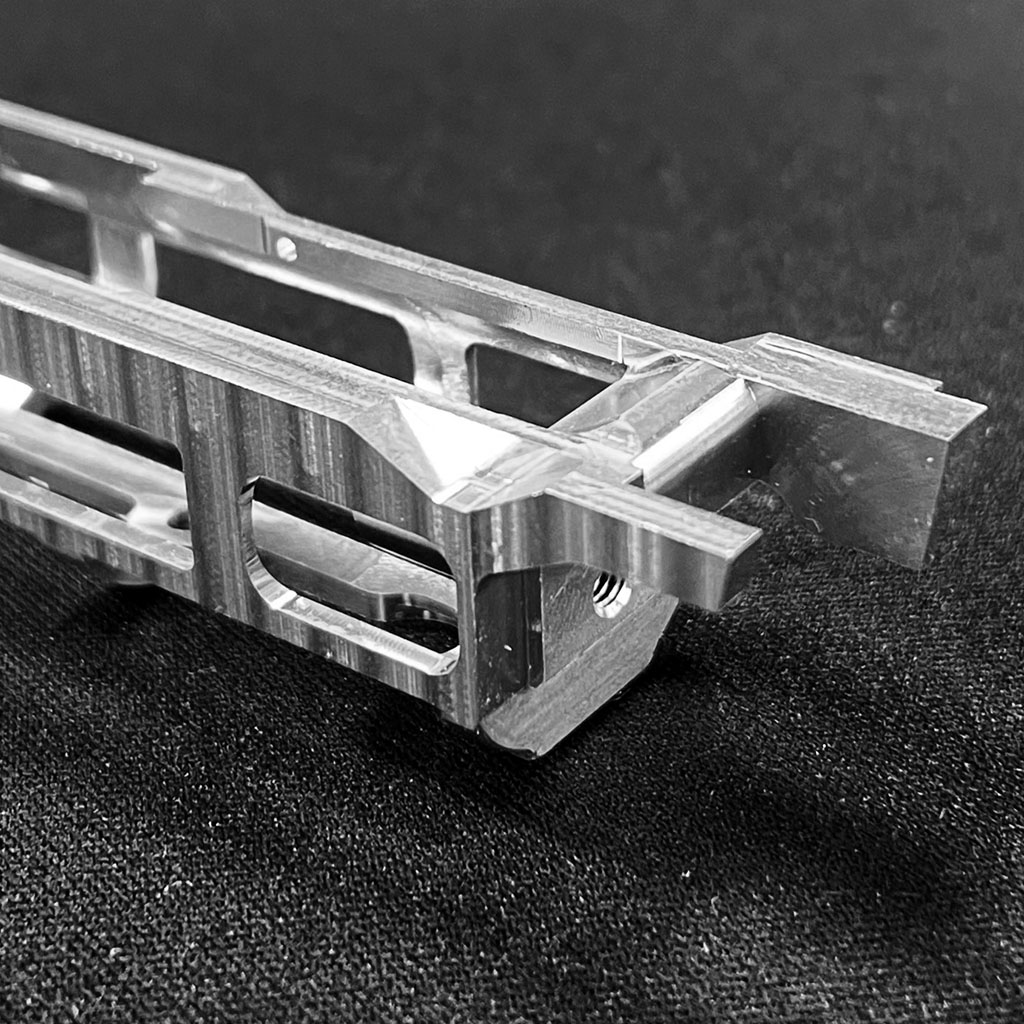
Custom Anti-Chatter Tool
We developed a unique cutting tool specifically designed to minimize chatter on the outer diameter, ensuring a smooth and accurate finish.